sheet metal blanking process Blanking and fine blanking are both shear-cutting fabrication methods; they create . wholesale cnc aluminum milling parts,SLD Precision offers top-quality CNC milling parts for various applications. With our advanced CNC milling capabilities, we deliver precise and .
0 · punching and blanking diagram
1 · perforating operation in sheet metal
2 · differentiate between blanking and punching
3 · difference between shearing and blanking
4 · difference between blanking and punching
5 · difference between blanking and piercing
6 · difference between blanking and fine
7 · blanking and piercing diagram
Look through the wide range of wholesale cnc aluminum lathe spare parts listings on Alibaba.com to find the right provider for your machining needs. All kinds of machining services are covered here.

punching and blanking diagram
Sheet metal blanking is a critical process in metal fabrication that involves the cutting or shearing of a shape from a metal sheet. This method plays a significant role in industries such as automotive, aerospace, and construction, where precision and accuracy are .Blanking and fine blanking are both shear-cutting fabrication methods; they create .The Sheet Metal Blanking Process – Step-by-Step Selection Sheet Metal Material Exam. Each project thoroughly analyzes the sheet metal types, considering strength, elasticity, and . The sheet metal blanking process involves a press, punch and die system working on a metal sheet. It takes the following form: i. The metal sheet is positioned over the die .
Blanking is a metalworking process involving cutting a metal workpiece into a predetermined shape, a foundational step in creating high-quality metal components. In this ultimate guide, you will discover the 6 key steps in the .Blanking is a crucial sheet metal fabrication process that involves cutting a flat sheet to create a flat piece or blank of specific shape and size. This process is essential in the early stages of . What is Blanking process? Sheet Metal Blanking involves cutting a desired shape from a metal sheet. The cut-out piece serves as the final product, and the remaining sheet .
Sheet metal blanking is a vital metalworking process that shapes thin metal sheets into precise tolerances for numerous applications. From material selection to finishing . Blanking and fine blanking are both shear-cutting fabrication methods; they create sheet metal parts using die and punch tooling. One main difference between typical Sheet Metal Blanking and fine blanking processes . Blanking is the process of punching raw metal pieces into specific shapes like a sheet or a strip. Learn the essential steps and benefits of the blanking process in sheet metal . What is Blanking process? Sheet Metal Blanking involves cutting a desired shape from a metal sheet. The cut-out piece serves as the final product, and the remaining sheet becomes waste. This process efficiently produces .
Blanking is a crucial sheet metal fabrication process that involves cutting a flat sheet to create a flat piece or blank of specific shape and size. This process is essential in the early stages of manufacturing, providing the foundation for subsequent forming, bending, or other processes.The answer lies in the meticulous sheet metal fabrication process. . 6 Steps to Blanking Process in Sheet Metal Meet Your Manufacturing Demands with Ease Efficiency Accuracy Discover Our Solutions. Pinterest Youtube Facebook Twitter. Services. Sheet Metal Fabrication;With the blanking die carefully designed, the focus shifts to preparing the sheet metal for the blanking process. Let’s see the essential steps involved in this preparation: Cleaning the Metal Surface: Before blanking, it’s crucial to clean the metal surface to remove any dirt, grease, or contaminants. This cleaning ensures a clean cut and .
Other, similarly natured processes include punching and piercing. Both remove material from a metal sheet but the end results differ from steel blanking. Punching is also a material removal process but rather than the final product being the punched out material, like in blanking, metal is removed so that the sheet metal itself is the final . Blanking is a process that precisely cuts out a product from sheet metal. A punch and die are used to remove the material through massive shearing forces. The desired shape, which is punched out, is used for specific applications while .
Sheet metal forming processes like blanking, stamping and bending are very commonly used in the manufacture of sheet metal parts and it takes a combination of different processes to manufacture sheet metal parts. Blanking is a common sheet metal manufacturing process used in the production from the
Sheet metal blanking refers to the process of punching raw metal pieces into specific shapes like a sheet or a strip. The final product received after this punching is called a blank, and thus, the name of the process is blanking. Manufacturers use this process in the fabrication to produce a workpiece with certain dimensions and geometry for .
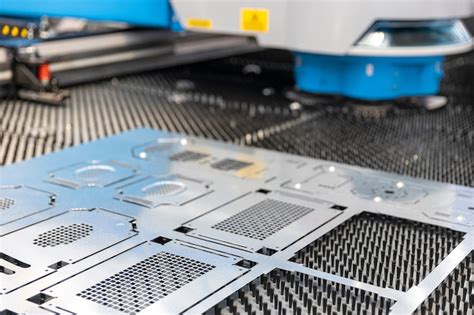
Sheet metal blanking is a fabrication process that I frequently rely on in our manufacturing operations. It involves sharing a piece of sheet metal to create individual parts, which are typically flat and may be of various shapes. The process utilizes a machine press and dedicated tooling, specifically a punch and a die. .
Sheet metal blanking process is a manufacturing process that is widely used in sheet metal forming and particularly in the electronics and automotive industries. The outcome and quality of the blanked parts are affected by various parameters such as the blanking clearance, the sheet metal mechanical properties and the wear of tools. .The Sheet Metal Blanking Process – Step-by-Step Selection Sheet Metal Material Exam. Each project thoroughly analyzes the sheet metal types, considering strength, elasticity, and corrosion resistance characteristics. The choice of alloys, whether malleable aluminum, robust stainless steel, or any other, depends on the requirements for the .The blanking process accounts for about 50% to 60% of the entire stamping process. Ⅰ. The basic process of sheet metal pressing process. The basic process is blanking and punching, which not only can process parts but also can process stamping process parts. Ⅱ. Precautions for the stamping parts design of the sheet metal pressing process. 1. The blanking process involves cutting out desired shapes from a larger sheet of metal. The cut-out piece is known as a “blank” and is used as the primary product, while the remaining sheet material is discarded. Blanking is widely used due to its ability to produce parts quickly and in large volumes.
The steel sheet metal blanking is widely used for the manufacture of mechanical parts for automotive industry. The general concept of blanking seems a simple one but governing parameters are many .
perforating operation in sheet metal
Blanking is a metal production process, during which a metal workpiece is removed from the primary metal strip or sheet when it is punched. The material that is removed is the new metal workpiece or blank. Profile of the blank piece . The shearing process such as the blanking of sheet metals has been used often to prepare workpieces for subsequent forming operations. The use of FEM simulation is increasing for investigation and .
of the sheet metal” Fig (2)”. Figure. (2). Different stage of the blanking process. Accurate knowledge of the failure process is essential for the selection of a suitable damage model. In the case of sheet blanking by shearing processes, numerous authors have studied the different physical mechanisms leading to the finalThe sheet metal stamping process is a strategic advantage that can set your business apart. Precision, efficiency, and innovation are at its core, driving the production of high-quality components. Precision, efficiency, and innovation are at its core, driving the production of high-quality components. Sheet metal blanking is a versatile and efficient metal fabrication process that involves cutting flat sheet metal into predefined shapes or profiles using specialized tools or dies. This article explores the applications of sheet metal blanking across various industries, highlighting its versatility and benefits in different manufacturing processes. Square sheared blanking is a fine process that uses specialized clamping tools to produce square-edged and contoured blanks. This process is a great way to create panels, casings, and any other component that requires a uniform square shape. Cutoff. This process combines metal cutting and metal blanking procedures to create highly specialized .
2. Introduction: Punching and blanking processes are sheet metal forming processes. In these two processes a finite volume of metal from a sheet is removed by using die and punch. The shape and size of the portion removed depends on the geometry of die and punch. Also the operation cost and time depends on die and punch design.Blanking is a cutting process in which a piece of sheet metal is removed from a larger piece of stock by applying a great enough shearing force.In this process, the piece removed, called the blank, is not scrap but rather the desired part.Blanking can be used to cutout parts in almost any 2D shape, but is most commonly used to cut workpieces with simple geometries that will be .What is blanking in sheet metal? It’s a process where specific shapes are cut from metal sheets, creating precise pieces used for further fabrication or
This document prescribes a model investigation the effect of potential parameters influencing the blanking process and their interaction. The blanking process optimization carried out by using Design of Experiment (DOE), Finite Element Method (FEM) with ANSYS Package, Simulation with ABAQUS-Explicit software, Blank soft Software and Neural Network Simulation in order to . During the blanking process, the sheet metal is placed on the die, and the punch is driven through the sheet metal, cutting out the desired shape. The force required to punch out the shape depends on the thickness and hardness of the material, as well as the size and shape of the punch and die. The sheet metal blanking process, in which a 5 mm thick circular plate is protruded into a fixed die. Figure 2 shows the schematic diagram of the sheet metal blanking process. Before the actual blanking process, in order to hold the workpiece rigidly in position, two vee-rings are pressed firstly into the workpiece along the contour.
The steel blanking process starts with a coil of sheet of steel, which is fed into a blanking press. This press, equipped with dies and punches, then cuts the metal into predetermined shapes. The precision of this process is crucial for producing uniform and high-quality blanks that will be further used in the manufacturing of various components.

aluminum fan shroud fabrication brazing
From precision CNC machining to complete fabrication, Pierce Aluminum delivers your project on spec, on time, and on budget. Our one-stop shops can handle any task from simple parts to final assembly of any size project.
sheet metal blanking process|difference between blanking and piercing