welding sheet metal gap There are 2 basic methods to MIG welding large gaps, the first is to use filler metal to help cover the gap that is cut to size to fill the gap and help make the weld a smoother . Topside Truck Box, Black, Double, Overall Width 72-1/4 In., Overall Depth 13-1/4 In., Overall Height 16 In., Storage Capacity 8.9 cu. ft., 12 Gauge, Mounting Style Bolt-On and Clamp-On, Locking System Keyed with Drill-Resistant Lock Core, Latch Mechanism D-Handle, 3-Point, Includes (2) Keys, Parts Bin, Body Material Aluminum, Cover Material .This selection of Lo-Side Truck Tool Boxes utilizes mounting brackets that don’t require drilling into the rails. Protect your investment with tamper-resistant, one-touch locks and watertight .
0 · welding tig sheet metal
1 · welding sheet metal using mig
2 · welding large gaps
3 · miller welding sheet metal
4 · how to weld sheet metal
5 · how to weld mig gaps
6 · gauge welding sheet metal
7 · filler metal for welding gaps
Universal Waterproof Camera Junction Box(4 Pack), Metal Electric Enclosure, Outdoor Camera Cover, Base Junction Box for CCTV Cameras, Bullet Security Camera Mount Bracket Hide Cable
There are 2 basic methods to MIG welding large gaps, the first is to use filler metal to help cover the gap that is cut to size to fill the gap and help make the weld a smoother . Preventing burn-through and warping when welding sheet metal is all about controlling the heat. Choose the right welding process and filler metal, and follow these . In this #WeldingWisdom video, David discusses tips and tricks for MIG welding various gaps. Tune in as he talks about ideal machine settings and techniques t. In this video I show how to bridge and weld up large gaps in sheet metal panels that contain odd shapes (not flat surfaces). This technique comes in very handy in any sheet metal repair or.
welding tig sheet metal
welding sheet metal using mig
Here, we’ll explore the sheet metal welding methods we use in our shop and explain what to expect from each one. Table of Contents. 1 Spot Welding. 1.1 Considerations for spot welding. 2 Tack Welding. 2.1 .Sheet Metal Gaps. When dealing with sheet metal, you must appreciate that strength and penetration are non-issues while heat and warping are a bigger headache. Designers of sheet metal pay close attention to the specificity of . Common Mistakes to Avoid in Butt Welding Sheet Metal. While butt welding sheet metal is a valuable and versatile technique, it is not without its challenges and potential pitfalls. Understanding and avoiding common .
Sharing my go to method for TIG welding up a gap. This is one of many ways to do it but I often end up with a weld that looks just as good as a perfect joint.
After it is right where it needs to be start weld consecutive spots weld (3 at a time) from one side to the other. Have an air wond on hand and cool the weld with air after the three spot welds. Below is a video how to weld . MIG welding sheet metal can be hard, as there’s a lot of heat involved in the process. The trick is finding a balance between the heat and time spent on it. . There are pros and cons to both ways, but if your metal is thinner than 3mm, you won’t need a gap. Gap. When fitting your sheet metal together, you can leave a small (like 1mm small .Welding aluminum is not hard at all, and extremely common. Braking aluminum presents different design criteria but again, not at all uncommon. There are alloys better for it as opposed to casting, machining, or extruding, of course. Some time at a metal fab job shop and I saw a lot of aluminum work come through, and had to do a lot of welding, too.
sheet metal fabrication quotation
welding large gaps
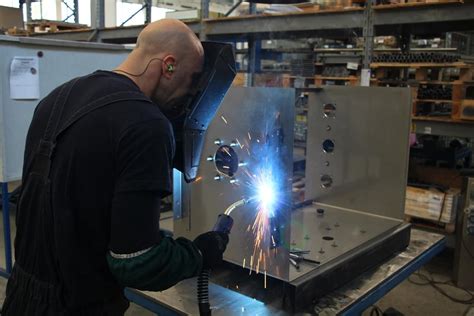
sheet metal fabrication san antonio
You are talking about sheet metal so penetration and strength won't be an issue. Heat and warping are a bigger factor to worry about. tommy, Feb 22, 2011. SHARE POST #9. . I have the best results with a gap close enough for the weld to penetrate the gap . I use a very fast tack weld to keep the heat down then do the criss cos method of tacks . 3. Adjust Your Torch Angle. Changing the torch angle when MIG welding goes a long way to preventing burn-throughs. Make sure you adjust the angle to shorten the distance between the tip and the metal, no matter the welding position you work in.This will make the arc more stable, giving you more control over the weld and lessening the chance of burn-through. Today we're going to demonstrate how to butt weld sheet metal using a Lincoln Electric mig welder. Like anything, there's a right way and a wrong way to butt. 6pcs 304 Stainless Steel Strips Thin Metal Strips Bendable Gap Filler Trim Welding Accessories Decorative Strips Finishing Sheet (11.8 x 1 Inch) Brand: KeaJuidy. 4.0 4.0 out of 5 stars 2 ratings . Metal Strips Stainless Steel Finishing Sheet Metal Gap Filler Trim Strip 12"x 1"x 0.02" Metal Shim Stock for DIY Craft Kitchen Stovetop 5 Pcs.
Welding sheet metal is a completely different ballgame. When you're trying to fuse two pieces of 22 gauge (.030) things can easily go south!In this episode w.
Imagine a welding process that minimizes distortion, enhances precision, and improves efficiency. Laser welding technology for sheet metal does exactly that, revolutionizing industries from automotive to high-tech electronics. This article explores the advantages of laser welding over traditional methods, detailing its superior heat control, speed, and flexibility. .When you weld thin sheet metal you want to go in short intervals because as you travel the heat transfers further down where you are welding, and when this happens your metal is already too hot when your weld arrives and you burn through. When I say weld in short intervals, what I mean is you are going to make a weld, and then stop for a second . The biggest mistakes with sheet metal welding are gap and heat. Flux core is way harder to do on thin metal. But with gas you should easily be able to weld down to 20 gauge (thinner with practice). Gap has to be tight between metal in order to bridge it quickly. If it is too large, by the time you develop enough puddle to bridge the gap, you've .
For thin sheet metal welding it can be 30 ampere while for thicker (e.g. 1/8” square groove weld)- it can go up to 220 ampere for example. GMAW-S gives low heat and makes it easy to use in all positions on sheet metal, low carbon steel, low alloy steel, and stainless steel sheet metal from 25 gauge (0.02 inch or 0.5 mm) to 12 gauge (0.1 inches or 2.6 mm). In this #WeldingWisdom video, David discusses tips and tricks for MIG welding various gaps. Tune in as he talks about ideal machine settings and techniques t. MIG welding sheet metal requires a combination of technical expertise, precision, and dedication to continuous improvement. By understanding the nuances of sheet metal welding, considering critical factors, .
miller welding sheet metal
That 16th of inch gap – which you can see as he shows a 1/16″ filler rod – you can fill, no problem. You can use a 1/16″ filler rod, although Kevin would probably use 3/32″ rod just to make sure he has enough metal to fill the gap and touch .
Corner welding joints are a popular weld in the sheet metal industry. When you have corner pieces that do not align together evenly, they are brought about, meaning you will need extra metal to add on and close the gap. As a rule of thumb, stick to welding all joints from the top as much as possible and welding inside a corner to create .
Sometimes it is "butted together" or 1/16 gap and other times the gap various out to 1/8 or 1/4 inch. On some of the closer spots, I tried to "bridge" the gap with a weld, but most of the time, the weld just "fell through" and didn't bridge or just made a larger hole. (arrggg !!)
Preventative measures – Choose a smaller wire diameter to match the thickness of the sheet metal being welded. Make sure your weld gap is as small as possible, less than 1/8” ideally. . Sheet metal patch – If you lose control of the blow-through altogether, you may need to remove the damaged area entirely and start over. Grind out the . In this video I show how to Mig weld any gap. This process is useful when you get your cuts off a little bit or your angles are off a little. This happens to. Enter the world of Flux Core Welding (FCW), a versatile technique with a unique approach to fusing materials.This method revolutionizes how welders approach sheet metal, from automotive repairs to constructing metal artworks.Grasping the principles of Flux Core Welding is essential for anyone interested in mastering this skill to achieve strong, durable, and reliable .
Those clamps are fine for thick gage metal but like 58 said,they have too big of a gap for sheet metal. We used them to line up a cab corner on the 56 and it sucked up BIG time and even after pounding the shemp out of the bead,still have a ditch to fill up.Some stretching of the piece with a slapper & dolly "should" help but I've learned my . I'm welding in 18g sheet metal for some rusted areas on my chevelle. I'm using a butt weld in all the areas and I am wondering how much of a gap I should have before I start welding the seam. . With a large gap the metal will suck in more making for more warpage. Plus with the right settings and technique you should get full penetration on .
How big of gap when butt welding quarter panels? 10-22-2008, 11:28 PM. I am going to weld some quarter panels on my 69 Camaro and I am wondering how much gap to set when doing a butt weld on this sheetmetal? . Today's auto sheet metal is a different critter than the old 30's and 40's cars I used to mess with (and messed up a few). Its thinner .
sheet metal fabrication saxonburg pa
You have to weigh that disadvantage with the advantage that having a gap will allow better weld penetration. My take: spend the time and get the panels perfectly flush. . welding 18 and 20 ga sheet metal. you want no gap. you are tig welding theses panels? if so you can use .035 mig wire and hammer weld the panels then file and metal finish 4*UL I made my own sheet metal styles and I still can't change the default corner size. If I start with a sheet and bend all 4 corners at the same time I can get the correct results. If I have a part with a couple falnges on it already it doesn't make a nice corner. Instead it makes a gap that is much too big to fuse with a TIG welder.

Outdoor Electrical Box, Waterproof Electrical Junction Box IP65 ABS Plastic Enclosure with Fan & Thermostat, Mounting Plate and Hinged Lid (15.7"H x 11"L x 5.9"W)
welding sheet metal gap|gauge welding sheet metal