how to calculate labour cost in metal fabrication An estimator for a job shop might propose the following fabrication outline for the part: 1. SHEAR—Shear 0.062 5052-H32 48" x 14" (5 per strip 10.179 x 9.207) 2. .
$84.99
0 · shop rates for metal fabrication
1 · sheet metal fabrication cost estimator
2 · sheet metal fabrication cost
3 · how to calculate metal manufacturing jobs
4 · how to calculate manufacturing rates
5 · how to calculate custom metal manufacturing
6 · factory manufacturing cost calculator
7 · custom metal fabrication labor rates
A CNC machine produces a product using coded instructions, without manual operation of the machine. These machines can be varied in size, function and design, and include lathes, milling machines and multi-axis machines. In this article, we will answer the question, “What is a CNC lathe machine?”
To determine shop rates, first identify your direct hourly labor rates, your fixed overhead costs, and your variable overhead costs. Direct hourly labor rates are the easiest to establish. They’re simply based on the actual . Multiply the total cost of direct labor for an hour’s production by the number of hours required to take a ton of metal through the fabrication process. The sum is the labor .Using the Steel Fabrication Cost Calculator is simple: Enter the length, width, and height of your steel structure in meters. Specify the density of the steel in kg/m³. Click the “Calculate” button. . Calculate every process and every resource, determine how much it costs you, and then compare this figure to the initial quote. Of course, you’re not just looking out for jobs .
To calculate this information, use the formula below: Machining cost= (hourly cost x cycle time for single piece) / efficiency. If the cycle time is 10 seconds with an 87% efficiency and hourly cost of .30, this formula will . An estimator for a job shop might propose the following fabrication outline for the part: 1. SHEAR—Shear 0.062 5052-H32 48" x 14" (5 per strip 10.179 x 9.207) 2. .You can largely determine your estimate by considering the following factors: Materials Used. You will need to present your project requirements to a fabricating company if you want customized metal pieces. In turn, the . Labour and Fabrication Cost Evaluation: After assessing the material cost, the next crucial aspect of estimating the cost of structural steel fabrication is evaluating the labour and .
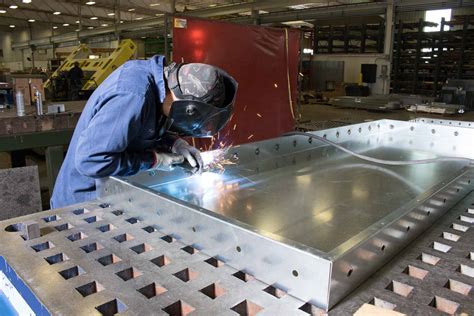
Metal fabricators turn unformed metal into a functional form, whether it’s flat sheets or intricate fence work. While the raw materials for metal fabrication sets a cost basis on the process, the labor cost involved in processing a ton of metal is an important consideration in deciding upon a sales cost for the fabricated material.We offer an online calculator, Metal Fabrication Price Calculator, to help you quickly determine cost of a fabrication project.It features: Up-to-date material price. Manufacturing price of processes such as blanking, welding, painting. . Calculate FAQs How is fabrication cost calculated? Fabrication cost is typically calculated by considering various factors such as materials, labor, overhead expenses, equipment costs, and any additional services required. It involves estimating the expenses incurred during the fabrication process. What is the fabricated item cost? The fabricated item cost depends on .The next step to estimate steel fabrication and erection costs is to calculate the material costs. This includes the cost of raw steel, such as plates, beams, columns, bars, and tubes, as well as .
We will discuss a sheet metal fabrication cost calculator using simple ideas and concepts. Step 1: Break Down the Production Cycle. . The thickness of the metal used for fabrication plays a vital role in the material cost and labor cost. If your project requires multiple materials, this may be associated with increased costs. . In general, for the same part, the unit cost for a batch of dozens can be several times higher than a batch of thousands. Batch size remains one of the most pivotal factors affecting costs. How to Reduce Sheet Metal Fabrication Costs. Here are some tips to reduce sheet metal fabrication costs. 1. Choose the right raw material
Piping Man-hours Estimation. Rough estimation of the order of magnitude (ROM) in the piping. In this post and the following, we will estimate the number of work hours required to assemble the welded piping as shown in the figure using three calculation methods.Q7: What other factors can affect steel fabrication costs? A7: Additional factors that can impact costs include the complexity of the design, labor costs, location, and market fluctuations in steel prices. Q8: Can I use this calculator for estimating steel welding costs? A8: This calculator primarily estimates the cost of the steel material itself. This method is based on labor studies for the various types and sizes of ductwork fabricated and the experience of the estimators knowledge of the sheet metal fabrication process and associated labor and installation. Production labor studies are most often used as the basis for determining labor cost.The document provides a cost estimate for structural steel fabrication work totaling 36 metric tons. It includes costs for materials, labor, machinery, taxes/profits, and calculates a final proposed rate per ton of Rs. 17,126.98. Labor costs make up the bulk of the estimate at Rs. 354,662. Additional assembly and machinery rental costs are also included.
Xometry offers a sheet metal fabrication cost calculator and discusses factors that affect fabrication costs. . Get detailed material quotes – The material type and grade make up the bulk of fabrication costs. Request labor rate estimates – Have the fabricator estimate production times and labor costs for your specific project.Everything you need to know about metal fabrication costs and prices in California. . We have collected data statewide to help calculate the average cost of metal fabrication in California. The following are average costs and prices reported back to us: Cost of Metal Structure or Object - Create Custom in California. 7.50 per hour (plus .The manufacturers and other fabricators can estimate welding costs either manually or using software programs. The following factors affect welding costs. They are labor cost, filler materials cost, machine cost, energy cost, etc. Labor Cost – It consists of hourly direct wage costs, employers’ social insurance charges, holiday pay, etc.
The sheet metal material cost that is in your computer program or that you calculate by hand. #7 (Total Fabrication Hours) . These should be your unadjusted values from your computer estimating program or if you have already put the net values into your database for shop labor, then those values are represented here.To sum up, we can roughly calculate the rough cost of manufacturing a one-kilogram aluminum die-casting part as follows: Cost of 1 kg of die-casting blank = material cost 4.3 SUD + cost of die-casting machine 1 USD + labor costs 0.08 . Because the direct labor costs may vary based on the operations required to produce the part, it is important to consider them by manufacturing process or activity. And if one employee will set up a machine before another .
Includes machine calibration, setup, and programming. Smaller jobs may have a lower setup cost per cut. Labor Costs: – per hour: Labor costs depend on the skill level of the operator and the complexity of the cuts. Consumables: – per hour: Plasma torch consumables (nozzles, electrodes) need replacement periodically.ESAB's QWPA is the best weld cost calculator to find the total weld cost analysis of your welding production. Just enter the weld data and click on calculate. . ESAB University is your online learning destination for welding and fabrication technology. Make personalized playlists of your favorite resources including videos, blogs, articles .However, budgeting for a steel structure requires a deep understanding of various cost components: material prices, fabrication, labor, transportation, and more. In this article, we'll provide a more accurate estimate of structural steel costs in Australia as of 2024, breaking down typical expenses for materials, fabrication, and construction .To calculate total manufacturing costs, you need to add up three key components – direct materials, direct labor, and overhead costs. First, identify the cost of direct materials, which includes all raw materials used in production. Next, calculate direct labor costs, which are the wages paid to workers directly involved in manufacturing.
stainless steel tissue box south africa
The cost of metal fabrication has dropped in recent years due to new processes and technology that are developing daily. . Labor - Skilled welder/fabricator fees of -0+ per hour. Delivery and installation needs to be factored in to total price as well.How to calculate the cost of sheet metal products considering cost of raw material, machining processes and the entire production cycle. EN; Home; Company; Products; Service; Academy; Work with us; . The formula to calculate the cost of the machining is the following: For example, with a cycle time of 12 seconds, efficiency 80,5% and a . See every fabrication job have many factors - design, location, finishing, time frame etc. Any how find the basic raw materials cost of the job. then count labour cost @ 30% - 40% of material cost, then calculate quantity of very skilled, skilled, semi skilled & unskilled man days.
Custom Metal Fabrication Series Part 4: Burden Labor. By definition, a manufacturing company’s burden rate is the allocation rate at which indirect costs are applied to the direct costs of labor or inventory. In essence, this helps custom metal fabricators calculate the total absorbed costs of the items they produce.Metals: The choice of metal directly influences the cost. Non-precious metals like brass or bronze are less expensive, while precious metals like gold or silver can significantly increase the cost. It’s vital to keep an eye on market prices, particularly for gold, given the considerable price disparity based on purity levels (14K, 18K, or 24K).
How to Calculate Hours Worked. Overtime for construction projects: [72.5/60] * 100 = 20.83% This is an extra cost of 20.83%. The customer agrees to pay whatever it costs, plus a profit to the shop. All the estimator needs to do is add up the expenses for material, machine hours, machine labor, and the shop’s consumables used to complete the job. The sales team then adds whatever margin is needed. All we need is a report on what the job cost.
shop rates for metal fabrication
sheet metal fabrication cost estimator
sheet metal fabrication cost

Used Filing cabinets – Choose from a wide range of used office storage furniture. wood and steel filing cabinets, wall units, bulk filers, filing units, bookcases, bookshelves, office cupboard and .
how to calculate labour cost in metal fabrication|shop rates for metal fabrication