welding sheet metal problems Now that we’ve covered the essential considerations for different arc welding processes, let’s discuss how to prevent and fix common . See more $54.90
0 · welding tig sheet metal
1 · welding sheet metal using mig
2 · welding sheet metal
3 · welding aluminum sheet metal
4 · sheet metal welding process
5 · miller welding sheet metal
6 · how to weld thin sheet metal
7 · how to weld sheet metal
During metal joining processes, weld symbols are meant to indicate different parts of the process. These symbols are usually found in fabrication and engineering drawings. A .
Each welding process requires specific precautions and equipment setup for a successful sheet metal weld. So, let’s discuss the preparation needed for each arc welding process before proceeding to the common problems with thin gauge welds. See moreNow that we’ve covered the essential considerations for different arc welding processes, let’s discuss how to prevent and fix common . See moreWelding thin metal is challenging. There is no denying that. But, if you practice and use the tips we shared in this article, you’ll get the best chance for success. After you inevitably burn through some scrap sheets of metal and warp others, you’ll gain more experience and learn . See more Preventing burn-through and warping when welding sheet metal is all about controlling the heat. Choose the right welding process and filler metal, and follow these .
Warping and distortion are common problems in sheet metal welding due to the high heat. Techniques such as staggered welding, preheating, and using a backing strip can help reduce these issues. Proper Bead Techniques. A good .
Being able to identify what the problem is and knowing how to remedy it can save you a lot of head-scratching and frustration. We’ll cover the most common weld defects you might encounter when welding, teach you . Porosity in sheet metal welding may be caused by the presence of materials such as paint, grease, rust and impurities. It can also result from the inadequate gas shielding when welding, impaired base metal, poor electrodes .
what color cabinets look good with black stainless steel appliances
Sometimes even professional welders may have trouble welding thinner materials. This is due to many factors that came into play. In this article, I am going to explain the fundamental ways of how to weld sheet metal that .
Table of Contents hide. 1 MIG welding. 2 TIG welding. 3 Stick welding. 4 Plasma Arc Welding. 5 Laser-beam welding. 6 Types of Welding Positions & Symbols. 7 Factors to be considered during sheet metal welding. .With higher thermal expansion and much lower thermal conductivity than carbon steel, stainless steels have a tendency to distort, warp and create all sorts of fit up issues. If you are welding stainless steel sheet metal for the first time you will .This problem is particularly acute when welding sheet metal because it will be both thinner and lighter, making it even more prone to warping. The positive aspect of this is that it is easier to sand, grind, or buff, making your preparation .
7 Common Sheet Metal Welding Problems and How to Fix Them Sheet metal parts are coveted for their simplicity, affordability and aesthetically pleasing build from thin plates of metals. The process efficiency, ease of .
Short, Quick Welds-When welding sheet metal with a MIG welder you do NOT want to try and run one long bead like when you’re welding heavier metal. Sheet metal warps easily and also can burn through easily. When welding a long bead on sheet metal you’ll put excessive heat into the panel and run the risk of the puddle falling through the panel. Welding is one of the most efficient methods used in connecting different pieces of metal to make a single piece. It is a significant technique in sheet metal fabrication to complete a part’s manufacture. However, there is a possibility that welds can fail, causing welding defects. Weld defects are common in sheet metal welding. These defects .Essential Equipment and Settings for Thin Sheet Metal Welding. . This is also an efficient technique to prevent common welding problems that arise when you are welding thin metal sheets. In backstepping, you will have to weld in the opposite direction of the overall seam, starting at the end of the joint and working your way back. . 11. Sheet Metal Tips. As mentioned in the introduction, sheet metal work is a different animal than steel beams. Any of the above practices can be useful in mitigating distortion in sheet metal, but there are additional practices that can come into play and perhaps save the day. These include: Water-Cooled Jig
Sheet metal welding can be easy if you apply the necessary technique. A welder does not have to have problems with adjusting the welding machine if they apply the necessary methods. Adapt your welding and with time and experience, . Did you know that TIG welding is the best option for sheet metal? The biggest problem any welder is going to face when it comes to sheet metal is the heat in.
Some of the problems with thin metal include burn through and excessive warping. You also have to avoid excessive heat affected areas while still ensuring the weld is strong enough. . MIG is one of the best ways to weld 20-gauge sheet metal. MIG welding is one of the simplest to use for welding. It is an arc welding process that where you . Plug welding kits include pre-cut blanks in multiple sizes plus a step-style bit for drilling sheet metal. Sheet metal patch – If you lose control of the blow-through altogether, you may need to remove the damaged area entirely and start over. Grind out the damage and cut a patch panel from another piece of sheet metal just large enough to .Problems With Welding Sheet Metal. If you are burning through the metal, you're not moving the torch fast enough and/or your welder is set too high. Solution: Move the torch faster, and/or reduce the amp setting of the welder and the lower the wire speed. Using a thinner wire (example; 0.30 instead of 0.35) will also help. Mig welding sheet metal problem. Jump to Latest 4K views 10 replies 7 participants last post by bonfire May 8, 2006. C. canela27 Discussion starter 81 posts
There is no hard and fast rule with the thickness under which you shouldn’t use stick welding.But there is a fair idea of what constitutes a thin metal and below which using stick welding might become difficult. A lot of people consider anything less than 3/16” to be thin so below this thickness stick welding can start creating problems or can become difficult to handle.Technology of welding sheet metal. Technology of welding sheet metal has direct impact on the design of the seam and the risk of damaging the sheet metal. Welding thin sheets i.e. to about 3 mm (cold rolled) to 4 mm (warm rolled) is among the most common, but also the most difficult sheet processing methods. Welding sheet metal is a completely different ballgame. When you're trying to fuse two pieces of 22 gauge (.030) things can easily go south!In this episode w.
what color cabinets go with stainless steel appliances
Sheet metal welding is a crucial fabrication process because it is one of the simplest ways to join cut-out pieces of metal sheets to create the desired shape. . In addition, the sheet needs to be correctly clamped to .
Welding sheet metal is a very critical process within the modern concept of manufacturing. The construction of metal structures, pipelines, and tanks is among the most common applications for sheet metal welding. . The more proficient you are in these genres of welding, the better you can cope with problems and difficulties confronting the .
A FEW TIPS FOR WELDING SHEET METAL ON CARS By John Kelly/Ghia Specialties. When welding a patch panel or fender flare on a car, I use either oxy-acetylene (gas welding) or wire-feed (mig welding), in that order of preference. . If your torch acts up once you’re set up the way you like, the problem is usually a dirty tip. Try welding two . For thin sheet metal welding it can be 30 ampere while for thicker (e.g. 1/8” square groove weld)- it can go up to 220 ampere for example. GMAW-S gives low heat and makes it easy to use in all positions on sheet metal, low carbon steel, low alloy steel, and stainless steel sheet metal from 25 gauge (0.02 inch or 0.5 mm) to 12 gauge (0.1 inches or 2.6 mm). Sheet metal is a different story entirely. Sheet metal is typically used for panels where being straight is important. Rocker panels, floor pans, patch panels, the straighter the better. Point being, the key to straight panels is heat mitigation. (Side note: you’ve just turned your car off and you hear a pinging noise from the engine bay .
what are corrugated metal sheet for roofing made of
Once you're set up and ready with your metal clamped into place you can start your tig welding tig welding sheet metal is a lot like tig welding any other kind of metal with only a few changes to technique . This video is a tutorial on welding thin metal with the UNIMIG VIPER 185Email: [email protected] & Bolt Welding. ProLine Pedestal Spot and Projection Welders. . High current, low force, expulsion and other systematic problems may cause cracks and holes in welds. Mislocated/Edge Welds. Edge welds are often the result of electrode misplacement, trouble with access to weld areas, or part defects. Sheet Metal Distortion. Problems with .
Warping and distortion are common problems in sheet metal welding due to the high heat. Techniques such as staggered welding, preheating, and using a backing strip can help reduce these issues. Proper Bead Techniques. A good welding bead is vital to a robust and durable weld. It’s crucial to control the bead’s size, shape, and consistency .
if it were me, i'd go for one that has the following features: 1.) bench-mounted. you can make your own stand much better than HF eer could. 2.) get at least 16 ga capacity. after about 16 or 14 ga, the brakes tend to get pricey pretty fast. 16 ga is about all that a HOME shop woudl ever need, but i find that the thicker capacity will help bend the heavier stuff easier. i.e. if . With a combination of these essential practices, one can master the art of TIG welding with ease. Get ready to MIG-nify your sheet metal skills and become a welding wizard. Understanding MIG Welding for Sheet Metal. MIG Welding for Sheet Metal is a process of joining thin metal sheets together using a MIG welder. The technique requires specific . By addressing common welding problems head-on, you can ensure successful welds, enhance the quality of your work, and ultimately excel in your welding career. . Welding Thin Sheet Metal With Flux Core: Expert Tips & Tricks; How To Braze Copper Water Pipe: Expert Tips for Beginners; Types Of Welding Positions: Master the Basics and Beyond .
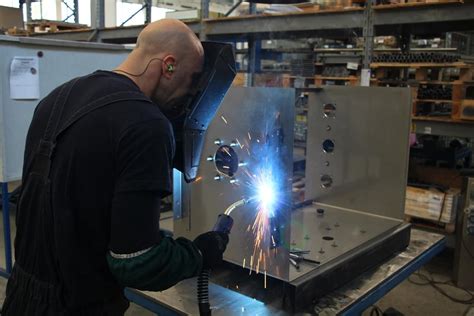
welding tig sheet metal
Find many great new & used options and get the best deals for ER-KNAPP #619-9 CABINET DOOR STAY, NON-HANDED, STEEL, BRIGHT NICKEL-PLATED at the best online prices at eBay! Free shipping for many products!
welding sheet metal problems|welding sheet metal using mig