sheet metal terminology pdf Sheet metal fabrication is the process of forming parts from a metal sheet by punching, cutting, stamping, and bending. 3D CAD files are converted into machine code, which controls a . Richards Welding and Metal Fabrication offers a variety of commercial steel .
0 · what is sheet metal operations
1 · types of sheet metal pdf
2 · sheet metal operations with diagrams
3 · sheet metal notes pdf
4 · sheet metal dimple terminology
5 · sheet metal basics pdf
6 · shearing operation in sheet metal
7 · neutral axis in sheet metal
Butt welding sheet metal is a fundamental welding technique that involves joining two metal sheets end-to-end. This process creates a strong and durable weld, making it an essential skill for fabricators and welders across various industries.
Sheet metal fabrication is the process of forming parts from a metal sheet by punching, cutting, stamping, and bending. 3D CAD files are converted into machine code, which controls a .SHEET METALWORKING. Cutting and forming thin sheets of metal usually performed as cold working. Sheet metal = 0.4 (1/64) to 6 mm (1/4in) thick. Plate stock > 6 mm thick. Advantage. .
List of sheet metal terminology, sheet metal definitions, sheet metal phrases, sheet metal terms and words used by sheet metal workers.Bending is one of the most common sheet metal fabrication processes and is used to create angular and u-shapes such as corners, tubes, and so on. Blanking. The process of cutting that .This lesson describes sheet metal concepts, terminology, and manufacturing equipment, and provides an overview of designing sheet metal parts with Autodesk Inventor. Sheet metal .
Sheet Metalworking Terminology. “Punch-and-die” Tooling to perform cutting, bending, and drawing. “Stamping press” Machine tool that performs most sheet metal operations. .Chapter 2 Classification and Description of Sheet Metal Forming Operations ... 5 2.1 Process V ariables ... 5 2.2 Sheet Metal Forming as a System ... 6DESIGN TIPS. OFFSET. Whenever possible, maintain minimum spacing of 2-2.5x raw material thickness from edge of cutout to bend radius tangency. Lesser spacing requires secondary .
This appendix is a glossary of terms and definitions associated with sheet metal forming. Skip to Main Content. Close. ASM International Home ; Handbooks Online ; Databases . ASM Alloy Center Database ; . Glossary, Sheet Metal Forming: Fundamentals, Edited By Taylan Altan, A. Erman Tekkaya, ASM International, 2012, p 233–266, .Edited by Taylan Altan and A. Erman Tekkaya ASM International® Materials Park, Ohio 44073-0002 www.asminternational.org Sheet Metal Forming FUNDAMENTALSFrom Centrifugal Casting to Metallurgy MetalTek offers a glossary providing a comprehensive list of engineering and metal working definition of terms. . A pebble-grained surface that develops in the mechanical forming of sheet metals with coarse grains. Oven, Drying. A furnace or oven for drying molds or cores.
Addeddate 2020-11-30 03:02:20 Identifier sheet-metal-handbook Identifier-ark ark:/13960/t5bd3qk96 Ocr ABBYY FineReader 11.0 (Extended OCR)
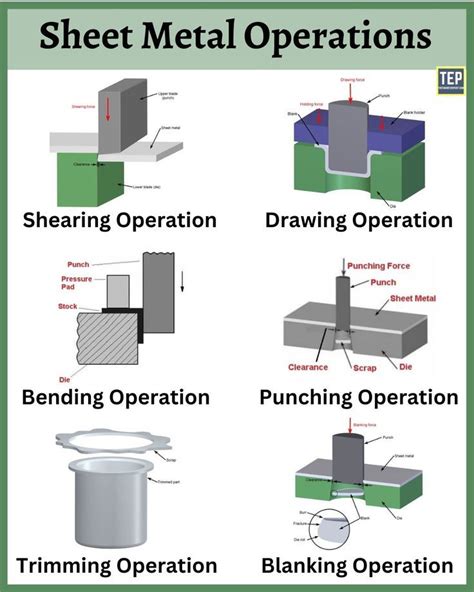
what is sheet metal operations
The document discusses key sheet metal design terminology: 1) Bend allowance is the extra length added to the flat sheet to account for stretching during bending, while bend deduction is the amount removed from flanges in the flat pattern. 2) K-factor represents the location of the neutral axis, where no stretching or compression occurs during bending. It is a ratio of the distance .10 Combined bending and tension of sheet 136 10.1 Introduction 136 10.2 Stretching and bending an elastic, perfectly plastic sheet 136 10.3 Bending and stretching a strain-hardening sheet 142 10.4 Bending a rigid, perfectly plastic sheet under tension 144 10.5 Bending and unbending under tension 145 10.6 Draw-beads 150 10.7 Exercises 151 11 .SHEET METAL CAD EXERCISES - Free download as PDF File (.pdf), Text File (.txt) or read online for free. The document lists 40 sheet metal CAD exercises numbered from 1 to 40 without providing any details about the content or objectives of each individual exercise. The exercises are presented in a list format without paragraphs or descriptions.Press Work Terminology - Free download as Word Doc (.doc), PDF File (.pdf), Text File (.txt) or read online for free. PRESSWORKING TERMINOLOGY 1. Air draw: A draw operation performed in a single-action press with the blankholder pressure supplied by an air cushion. Annealing: A process involving the heating and cooling of a metal, commonly used to induce softening.
The following are some terminology that are used in sheet metal. Designers need to adhere to machinery guidelines when designing for bending. Bends can be characterised by these parameters. Some critical dimensions that need to be considered when setting up sheet metal in CAD software are sheet metal thickness, the k-factor, and bend radius. Sheetmetal is simply any metal alloy that stores as a sheet, or is coiled as a matter of convenience to ease handling–some coils stretch for more than a mile. Although no firm break exists between categories, for most alloys, sheet thickness ranges from 0.2 to 6 mm. Plate refers to thicker material, while foil denotes thinner (Fig. 1).
Application of sheet metal components includes Aircraft industry, Automobiles, Construction work and many other applications such as appliances, . given below in terms of the stock c = 5% of t eel, c= 6% of t c= 7% of t c= 10% of t VI. Tool Raw Material Raw material selection influences three following areas. 1) Tool Life .
Corner bead: A strip of formed sheet metal or plastic placed on outside corners of drywall be-fore applying drywall 'mud'. Can be either square or bull nose (round). Counter flashing (aka “Z” flashing): A galvanized sheet metal flashing used at the roofline to cover shingle flashing (“L” flashing) and used to prevent moisture entry .5 • Blend Create a sheet metal wall by blending several sections sketched in parallel planes as shown in Figure SM.10. Figure SM.10 Base Feature, Blended Wall • Flat Sketch the boundaries of the wall (Fig. SM.11). Figure SM.11 Feature, Flat Wall • Offset Create a wall that is offset from a surface (Fig. SM.12). Figure SM.12 Base Feature, Offset Wall .CONTACT. 1243 Schamberger Freeway Apt. 502Port Orvilleville, ON H8J-6M9 (719) 696-2375 x665 [email protected] Source: www.pinterest.ca I want to practice please. Sheet metal 2d drawings for practice pdf 2012 solidworks help dxf/dwg files (*.dxf *.dwg files) another area where we can practice our cad skills is to draw the neutral axis .
You can flatten all the bends of a sheet metal part at once. Creating a Sheet Metal Drawing. Now create a drawing of the sheet metal part. Start with an isometric view of the folded model, and then add a view of the unfolded model. .This document defines and describes the primary structural components and terminology for a typical ISO shipping container. It lists over 30 structural elements and features, including corner fittings, corner posts, door headers, .Sheet-Metal Forming Processes Process Roll forming Stretch forming Drawing Stamping Rubber-pad forming Spinning Superplastic forming Peen forming Explosive forming Magnetic-pulse forming Characteristics Long parts with constant complex cross-sections; good surface finish; high production rates; high tooling costs.When developing sheet-metal patterns, ensure you add sufficient material to the base dimensions to make the seams. Several types of seams used to join sheet-metal sections are discussed in this section. There are three types of lap seams: the PLAIN LAP seam, the OFFSET LAP seam, and the CORNER LAP seam (fig. 2-66).
Sheet Metal Basics - Free download as Word Doc (.doc / .docx), PDF File (.pdf), Text File (.txt) or read online for free. This document provides guidelines for sheet metal forming and bending. Some key points include: 1) Dimensions should generally be from a feature to an edge and avoid feature-to-feature dimensions over multiple planes to control tolerance accumulation.Sheet Metal Forming: Fundamentals describes the changes that occur in sheet metals during forming operations and explains how to model and analyze them usi . The book also includes a collection of flow stress curves and a glossary of relevant terms. For information on the print version, ISBN: 978-1-61503-842-8, . View Chapter PDF Link PDF .
10 Combined bending and tension of sheet 136 10.1 Introduction 136 10.2 Stretching and bending an elastic, perfectly plastic sheet 136 10.3 Bending and stretching a strain-hardening sheet 142 10.4 Bending a rigid, perfectly plastic sheet under tension 144 10.5 Bending and unbending under tension 145 10.6 Draw-beads 150 10.7 Exercises 151 11 .jigs - Free download as Powerpoint Presentation (.ppt / .pptx), PDF File (.pdf), Text File (.txt) or view presentation slides online. This document provides terminology and descriptions related to press working and presses. It defines a press as a machine tool that changes the shape of a workpiece by applying pressure. It then describes common press types and accessories like .Press working Terminology (1) Principle elements of metal machining (1) Reamers and its types (1) Rolling (1) Safety Precautions and Measurements (1) Sand Casting Processes (1) Sheet Metal Cutting and Forming operations (1) Shell Moulding (1) Special Casting Processes (1) terminology of Dies (1) Types of Chips (1) Types of Drilling Jigs (1 .HVAC TERMS & DEFINITIONS. A.S.T.M. Standards issued by the American Society of Testing Materials. ACCA Air Conditioning Contractors of America. . Just peel, stick and fasten with sheet metal screws. Fahrenheit A temperature scale in which water freezes at 32 degrees and boils at 212 degrees at normal atmospheric pressure.
Sheet Metalworking Terminology 1. “Punch-and-die” • Tooling to perform cutting, bending, and drawing 2. “Stamping press” • Machine tool that performs most sheet metal operations 3. “Stampings” • Sheet metal products 13Terminology 1: Bed: The bed is the lower part of the press frame that serves as a table to which a Bolster plate is mounted. 2: Bolster Plate: . The sheet metal working process in general is known as cold stamping as the sheet during working on it is always in cold state as

types of sheet metal pdf
To weld sheet metal with solid wires, use electrode positive (EP, or reverse polarity). Don’t attempt to weld thin materials like sheet metal with flux-cored wires, which put more heat into the base metal. Forget the larger 1/8-inch tungsten electrode and use a .
sheet metal terminology pdf|what is sheet metal operations